Building Better. Together.
Advanced Technology. Simple Solutions.
Advancing Solutions in…
Thompson Solutions Group is...
- Innovative
- Knowledgeable
- Dependable
- Timely
- Efficient
- Sustainable
-
Quality
Thompson Solutions Group employs cutting-edge technology and extensive vendor relationships to provide the best products at the best prices with the best service. We’re guided by lean manufacturing principles that aim for efficient installations with minimal waste, and we’re committed to sustainability – doing what’s best for business and the communities we serve.
-
Trusted
The Thompson Solutions Group has a rich history spanning more than 90 years of leading by example and sparking innovation across the Midwest and throughout the spectrum of trades: electrical, mechanical, automation and robotics, temperature control, metal fabrication, plumbing, HVAC, industrial piping, life safety and security, managed IT, and architectural metal.
-
Responsive
The Thompson Solutions Group is wired for service and passionate about providing custom solutions to meet your specific needs. Our customer-focused experts are engaged and empowered to listen, seek to understand your goals, and help you accomplish your mission. And we’re committed to strong client relationships, clear communication, and customer satisfaction with every project, product, service, and contact.
Quality
Trusted
Responsive
Careers with Thompson Solutions Group
People Are Our Strength
Fast-Paced and Flexible
Advancing communities in the Midwest
Sioux City
Sioux Falls
Omaha
Commercial/Office
From retail storefronts to restaurants, hotels, office buildings, multi-unit residential complexes, data centers and more, commercial services have been the foundation of Thompson’s business.
Industrial/Manufacturing
Our expertise in innovation and cutting-edge technology has long helped industrial sites and manufacturing centers grow and streamline their productivity through advanced processes, automation and robotics.
Agricultural
From retail storefronts to restaurants, hotels, office buildings, multi-unit residential complexes, data centers and more, commercial services have been the foundation of Thompson’s business.
Professional
Small to medium-sized businesses benefit from Thompson’s focus on technology, as well as its premium electrical contracting, managed IT and training services.
Education
Face the challenges of today’s world with Thompson’s safety, security and interactive tech solutions. We’re a partner in education for your local elementary schools through the region’s top colleges and universities.
Government
We provide public service agencies with the best value for their taxpayers’ money while adhering to the varying codes and regulations at the city, county, state and federal government levels.
Healthcare
Streamline your hospital, clinic, nursing home, treatment center, hospice home or lab facility with effective and efficient technological solutions that address today’s security challenges, enhance infection control and promote seamless patient care coordination.
Residential
Our residential electricians are available 24/7 for all kinds of electrical work, including electrical installation for new construction, electrical service upgrades or updates for remodeling projects, and repairs during or after emergencies or power outages.
Stories of Success
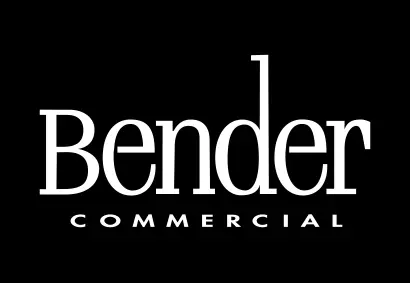
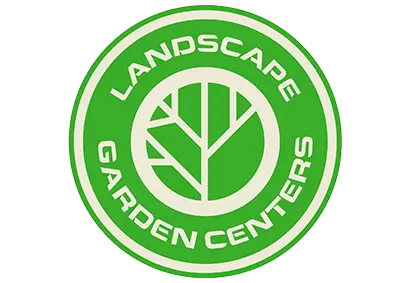
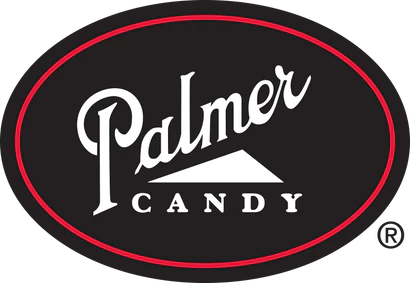
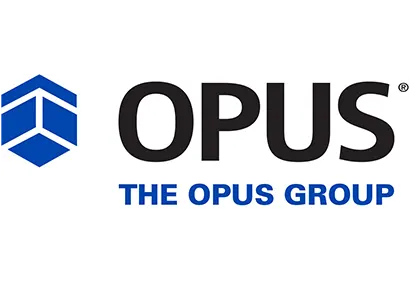